CytodexTM microcarrier cell culture process in WAVETM bioreactor
Summary
The WAVE Bioreactor system is mostly used for the culture of suspended cells. However, a variety of cells for cell therapy and vaccine production are anchorage dependent and require an attachable growth surface. In this study, Cytodex microcarriers were used in the CellbagTM bioreactor to amplify Madine-Darby Canine Kidney (MDCK) and Vero cells. To optimize cell attachment, different shaking mixing conditions of the two cell lines were tested. We found that media components have a significant effect on cell attachment; for example, MDCK and Vero cells in low serum media can be attached to microcarriers by intermittent and continuous shaking. However, under serum-free conditions, Vero cells can achieve high adherence rates under intermittent shaking mixing. MDCK cells grown in the WAVE Bioreactor system can be amplified to 2 L and 10 L working volumes. The cells reached a maximum density of 3 x 106 cells/ml. Vero cells were cultured on Cytodex 1 and Cytodex 3 microcarriers at a 2 L working volume, achieving a maximum density of 1.4 x 106 cells/ml in serum-free conditions. The same density of Vero cells can be obtained under the same conditions as the spinner flask, and the cells grow faster in WAVE.
The data shows that the WAVE Bioreactor system is a universal platform for successful microcarrier culture of MDCK and Vero cells, which can be easily scaled up and is a fast and convenient alternative to traditional stirred tank bioreactors or rotary bottles.
Introduction
Unlike cell culture in Roller Bottles, the culture of adherent cells on microcarriers makes it relatively easy to scale up the production process. In addition, microcarriers enable cells to be expanded in bioreactors. Compared to plastic culture vessels such as small T-bottles, bioreactors provide better control of process parameters, reducing labor intensity while reducing pollution. Danger. The use of disposable bioreactors reduces investment costs, increases flexibility (simplifies operations such as rotation between batches), and eliminates the need for production vessel cleaning validation.
The WAVE Bioreactor system is a disposable fermentation device designed for human, animal, plant and insect cell culture and can be used for bacterial and fungal cultures. The WAVE Bioreactor system does not require cleaning or sterilization, which reduces the need for process validation in biopharmaceutical production. Although the WAVE Bioreactor system is mostly used for the culture of suspension cells, the research in this paper indicates that the WAVE reactor is also suitable for the culture of adherent cells on microcarriers.
This article describes the culture of MDCK and Vero cells on Cytodex microcarriers in the WAVE Bioreactor system. We conducted in-depth studies on the parameters necessary for microcarrier culture such as optimal shaking mixing conditions and working volume range, cell attachment efficiency, maximum cell density, and the feasibility of scaling from 2 L working volume to 10 L. The WAVE Bioreactor system and the spinner flask culture were compared and evaluated using cell-specific parameters such as attachment, growth rate, and maximum cell density. The general procedure for adherent cell culture in the WAVE Bioreactor system is shown in Figure 1.
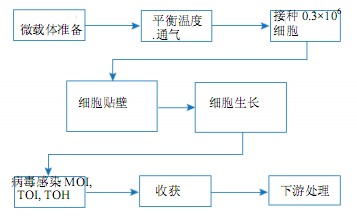
Figure 1. Microcarrier culture process flow diagram in the WAVE Bioreactor system
Materials and Method
Cell lines, media and stock solutions MDCK cells were obtained from ECACC (Nr. 84121903). The cells were cultured in UltraMDCK (12-749Q, Lonza) medium containing 2% FBS (CH30160.03, HyClone). During inoculation of cells in conventional culture and microcarrier culture in T-flasks and cell factories, MDCK cells were first washed with PBS-EDTA (E8008, Sigma Aldrich) and then digested with accutase enzyme (L11007, PAA Laboratories).
Vero cells are from ATCC (Nr. CCL 81). The culture was carried out using a serum-free medium based on DMEM/Ham's. Cell growth was performed in a WAVE Bioreactor system using medium containing 0.2% Pluronic F68 (Sigma Aldrich). Trypsin (Gibco BRL) was used to digest cells in routine cultures in T-bottles and cell factories. Soybean (1 mg/ml in PBS)-derived trypsin inhibitor STI (Sigma Aldrich) and EDTA were used for termination of trypsin digestion. Vero cells were digested with 0.02% EDTA prior to inoculation into the microcarriers. Then add the medium.
Culture Vessels In conventional cultures, MDCK cells were grown in T-bottles and multi-layer cell plants (Corning Life Sciences, Sigma Aldrich) for vaccination preparation.
In conventional cultures, Vero cells are grown in T-bottles and multi-layer cell plants for vaccination preparation. Cell culture was carried out in a 125 ml Techne spinner (Spinner Flask, Bibby-Scientific Ltd) at a working volume of 60 ml. The Spinner Flask spinner was stirred and mixed at 50 rpm.
The microcarrier Cytodex 3 microcarrier was used for adherent culture of MDCK cells, and Cytodex 1 and Cytodex 3 were used for adherent culture of Vero cells. The microcarriers are hydrated and autoclaved in a glass container in a siliconized country. After washing 3 times with PBS containing no Ca2+ and Mg2+ ions, the microcarriers were autoclaved at 121 °C for 15 min and stored aseptically at 4 °C. The microcarriers were first washed with media and transferred to the Cellbag for equilibration 24 h prior to inoculation. The amount of Cytodex 1 and Cytodex 3 used was 3 g/l. In order to prevent the microcarriers from adsorbing to the glass surface, both the transfer bottle and the spinner bottle were siliconized by Sigma Cote (Sigma Aldrich).
Bioreactor for MDCK and Vero cells The WAVE Bioreactor system consists of a rocking platform with a disposable plastic cell culture bag equipped with a CO 2 gas mixer (CO2MIX20) or a WAVEPODTM control tower for pH, temperature, oxygen And mix. MDCK cells were cultured in the WAVE Bioreactor System 20/50 of Cellbag-10 L and Cellbag-50 L. Vero cells were cultured in Cellbag-2 L and Cellbag-10 L in WAVE Bioreactor System 20/50. The WAVEPOD control tower is used for monitoring and feedback control of parameters such as pH, temperature, oxygen and mixing.
The staining solution was subjected to nuclear counting of MDCK and Vero cells using 0.1% crystal violet cell lysis buffer dissolved in 0.1 M citric acid. Trypan blue (0.1% dissolved in PBS) was used to determine cell viability. For Vero cells, Hematoxylin Sumu violet dye solution (Carl Roth GmbH) for cell fixation and microcarrier culture microscopy from 0.9 g hematoxylin, 0.18 g NaIO 3 , 15.45 g Al K(SO4) 2 ×12 H 2 0, 45 g hydrated Chloralhydrate (Carl Roth GmbH) and 1 g of citric acid monohydrate dissolved in 1 L of distilled water.
Cell Culture- MDCK Cells MDCK cells were passaged twice a week from 1:5 to 1:6. For conventional cell culture and microcarrier inoculation, MDCK cells were first washed with PBS-EDTA and then detached from the microcarriers by incubation with Accutase enzyme at 37 ° C for 30 min. We took a portion of the exfoliated MDCK cell sample and measured the cell viability using CEDEX (Innovatis), which was used to calculate the number of cells required to reach the target seeding density. The suspension cells were added to the Cellbag using a transfer vial.
Cell culture - Vero cells Vero cells were passaged twice a week from 1:3 to 1:4. Under these conditions, trypsin-digested microcarriers are more difficult to inoculate because trypsin easily impairs cell attachment and affects cell spreading on the microcarriers. Therefore, the cells were digested from the surface of the cell factory with PBS without Ca 2+ and Mg 2+ containing 0.02% EDTA. The 10-layer cell factory was washed with PBS, and the cells were digested with 100 ml of EDTA solution and incubated at 37 ° C for 20 min. After incubation, we added 500 ml of cell culture medium and pooled the inoculum of all cell layers. We took a portion of the cell samples and counted them in a cell blood cell counter. Cell viability was determined using trypan blue staining (0.1% trypan blue in PBS). Next, we determined the amount of suspended cells needed to reach a specific seeding density, and then the cells in the transfer flask were added to the Cellbag by sterile welding.
Samples were taken daily to determine density and morphology. Prior to sampling, the reactor agitation rate was appropriately increased to ensure uniform suspension of the microcarriers (16 rpm and 12 ° for Cellbag-2 L and 18 rpm and 5 ° for Cellbag-10 L). After increasing the agitation rate for 2 min, 4 ml of the carrier suspension was taken from the sampling port while the reactor was continuously shaken. The agitation parameters of the reactor are then returned to the operating parameters at the time of cell culture and the sample is transferred to a centrifuge tube. The microcarriers were first sedimented, the supernatant was discarded, and the microcarriers containing Vero cells were resuspended in 1 ml of 0.1 M citric acid solution containing 0.1% crystal violet, and then incubated for 1.5 h. The released nuclei were counted using a hemocytometer. For MDCK cells, the vector was resuspended in citrate and Triton X-100 solution containing 0.1% crystal violet. The vector suspension was then vortexed for 30 s and the nuclei were counted using a Bürker chamber.
The 0.5 ml Vero cell microcarrier suspension was transferred to a small centrifuge tube. After the microcarriers were settled, the supernatant was discarded, and Vero cells attached to the microcarriers were fixed and stained with a 0.3 ml hematoxylin solution. The microcarriers were magnified 100 times under a microscope for observation and microphotographing.
The optimal working volume for microcarrier culture determines the optimal working volume for Cellbag-10 L and Cellbag-50 L. The recommended working culture volume in the culture bag is 40% of the maximum recommended volume (ie 2 L for Cellbag-10 L and 10 L for Cellbag-50 L). The microcarrier density was 3 g/l Cytodex 3 and the seeding density was 0.3 x 10 6 cells/ml. For each Cellbag and culture volume, the following shaking conditions were tested: 10 rpm and 5 o , 12 rpm and 5o, 14 rpm and 5o and 12 rpm and 6 o .
Optimal mixing conditions for microcarrier cultures were studied for optimal mixing of Cellbag-10 L with a working volume of 2 L. The medium and microcarriers were equilibrated in Cellbag-10 L for 2 h at 37 ° C and 5% carbon dioxide aeration. Inoculation was carried out at an initial density of 0.3 x 106 cells/ml, and continuous shaking was used in the cell-microcarrier attachment phase. After the cells were grown for 18 h to reach a cell density of about 0.6×10 6 cells/ml, the shaking speed was gradually increased in a stepwise manner. The initial shaking speed of 12 rpm was tested at 5o, 6o and 7o respectively. The shaking speed is gradually increased every hour in a stepwise manner until the cells begin to fall off the microcarriers.
Results and discussion
Determination of Optimal Working Volume and Mixing Rate for Microcarrier Culture When we used 20% to 80% of the maximum working volume of Cellbag, microcarrier cultures produced a uniform distribution of microcarriers (Figure 2).
Figure 2. Optimal working volume for microcarrier culture
At a maximum working volume of Cellbag with a working volume of less than 20%, some of the microcarriers may stick to the Cellbag, while more than 80% of the working volume may result in uneven microcarrier mixing.
Figure 3 shows the uniform mixing of the microcarriers obtained at shaking angles of 5o, 6o and 7o. A shaking speed of more than 8 rpm produces a uniform microcarrier mixing effect. MDCK cells were detached from the microcarriers at a shaking speed of 16 to 20 rpm.
Figure 3. Determine the minimum mixing conditions required to obtain a uniformly mixed microcarrier solution, and the maximum mixing conditions before cells are detached from the microcarriers using Cellbag-10 L. The Cellbag-10 L has a mixing condition similar to the Cellbag-50 L. The 50 L Cellbag uses 6 rpm and 7o for uniform mixing.
MDCK cell attached microcarriers (2% FBS)
The purpose of the study was to find the optimal conditions for attaching MDCK cells to Cytodex 3 microcarriers in WAVE Bioreactor System 20/50 (cell culture volume up to 25 L). We compared 3 species in the adherent phase 4 h before culture. Different ways of mixing:
1) Intermittent mixing: Mix intermittently at 12 rpm and 6o for 2 min every 30 min (Fig. 4), stop shaking at other times; use continuous shaking after 4 h (10 rpm and 5o)
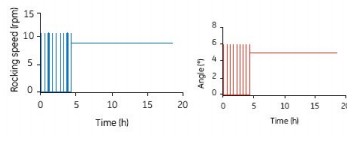
Figure 4. Intermittent mixing for 2 min (12 rpm and 6o) every 30 min in the first 4 h of the 10 L Cellbag, with continuous shaking (10 rpm and 5 o) after 4 h
2) Semi-batch mixing: Accelerate mixing for 2 min at 12 rpm and 6o every 30 minutes, and keep shaking at 6 rpm and 3.3o at low speed for other times. Continuous shaking after 4 h (10 rpm and 5o)
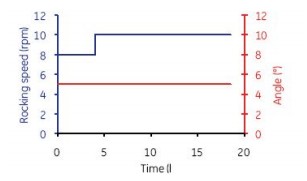
Figure 5. Accelerate mixing for 2 min every 30 minutes (12 rpm and 6o), then keep mixing at low speed (at 6 rpm and 3.3o), so mix for 4 h in a semi-batch. After 4 h, the mixing parameters were set to 10 rpm and 5o continuous shaking.
3) Continuous shaking mix: shaking speed 8 rpm and 5o. Continuous shaking after 4 h (10 rpm and 5o)
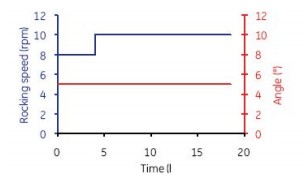
Figure 6. The first 4 h of culture in Cellbag-10 L was continuously mixed at 8 rpm and 5o. 4 h after mixing parameter is set to 10 rpm and 5 º.
The microcarriers were used in an amount of 3 g/l of Cytodex 3, and the inoculated cell density was 0.3 x 106 cells/ml. The culture conditions were 37 ° C, pH 7.3, 5% CO 2 , and the dissolved oxygen level was monitored by a fiber-dissolved oxygen electrode. The medium contained 2% FBS. The total cell density was measured every hour and stained with crystal violet, and the suspended cells and dead cells in the supernatant were stained with trypan blue. MDCK cells were attached to the surface of the microcarriers 1 h after inoculation (Fig. 7A). After 3 h of culture, 85% of the inoculated cells were attached (Fig. 7B). After 18 h, the cells spread on the surface of the microcarriers and began to grow (Fig. 7C).
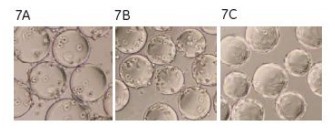
Figure 7. Photomicrograph of MDCK cells attached to microcarriers. After 3 h of culture, 85% of the inoculated cells were adherent (7B). After 18 h, the cells spread and began to grow (7C).
Although continuous mixing enabled a more uniform distribution of cells on the microcarriers, no significant differences in cell adherence and growth were observed between the batch, semi-batch, and continuous shaking mixing steps (Figures 8, 9, and 10). . Under the low serum conditions of 2% FBS, different mixing steps showed similar results, and the adherence conditions of MDCK cells were very durable.
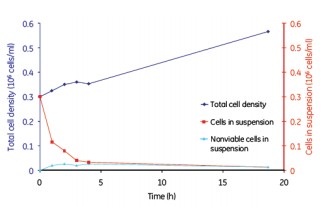
Figure 8. MDCK cell microcarrier adherence in a batch mode
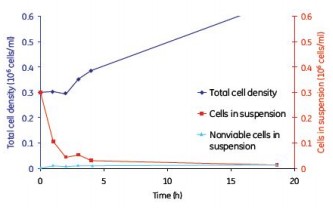
Figure 9. MDCK cell microcarrier adherence in a semi-batch mode
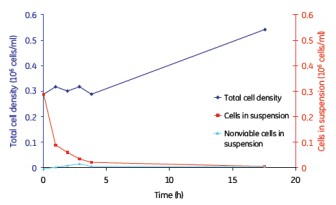
Figure 10. MDCK cell microcarrier adherence in a continuous mix
Vero cell attached microcarrier
We used different shaking protocols and media composition to study the attachment of Vero cells to Cytodex 3 microcarriers. Cell culture was performed in a Cellbag-2L at a working volume of 600 ml. The continuous shaking parameters were set to 12 rpm and 5.5o; intermittent shaking at 16 rpm and 5o for 2 min; then set to 0 rpm and 0o to stop shaking for 18 min. After 6 h, all of the above shaking modes were switched to a continuous shaking mode of 12 rpm and 18o. Figure 11 shows that approximately 90% of cell attachment is obtained during continuous or intermittent shaking mixing under serum-containing conditions. Under serum-free conditions, 80% attachment was obtained by batch mixing and 30% attachment by continuous mixing.
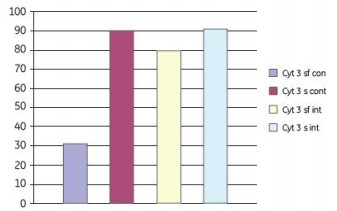
Figure 11. Effect of serum-free (sf) and serum-containing (s) media on the attachment of Vero cells to Cytodex 3 microcarriers. In the adherent phase, a combination of continuous shaking (cont) and intermittent shaking (int) is employed. The adherence of cells on the microcarriers 24 h after inoculation is shown in the figure.
Growth and amplification of MDCK cells (2% FBS)
To investigate the scalability of MDCK cell expansion in the Cellbag bioreactor, the maximum cell density and cell growth rate of Cellbag-10 L and Cellbag-50 L were compared between two different sized bags. The working volume of the bag is 40% of the maximum working volume (2 L in Cellbag-10 L and 10 L in Cellbag-50 L).
The microcarriers were used in an amount of 3 g/l of Cytodex 3, and the seed density was 0.3 x 106 cells/ml. MDCK cells were mixed at a shaking speed of 8 rpm and a 5o angle. During cell culture, the shaking speed was gradually increased from 8 rpm to 14 rpm in a stepwise manner while maintaining the same angle. The culture temperature was 37 ° C, pH 7.4, and the dissolved oxygen level was monitored, and the cell culture medium contained 2% FBS.
After the initial lag phase, the final cell density reached 3 x 106 cells/ml, similar to the maximum cell density obtained in a spinner (Spinner Flask). The cell growth conditions of the 2L and 10L culture volumes were similar, thus showing good scalability (Fig. 12).
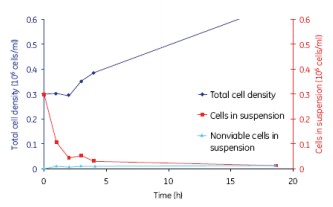
Figure 12. The growth of MDCK cells was similar for the 2 L and 10 L culture volumes, indicating a good scalability of WAVE.
Growth of Vero cells in serum-free culture conditions on Cytodex 1 and Cytodex 3 microcarriers
Vero cells inoculated at 4 x 105 cells/ml were cultured in Cellbag-10 L containing 2 L of serum-free medium, respectively, in Cytodex 1 and Cytodex 3. The cells were mixed for 6 h with intermittent shaking (16 min at 16 rpm and 4.5 o, then stopped shaking for 18 min at 0 rpm and 0 o). Figure 13A shows that Vero cells were completely spread after 6 h of culture on Cytodex 3, but the cells were not spread out on Cytodex 1 (Fig. 13 B). In order to increase the spreading of Vero cells on Cytodex 1, the culture was stopped for 2 h, improving the spreading of cells on Cytodex 1 (Fig. 13 C). Thereafter, both cultures were continuously cultured at 37 ° C with continuous shaking (11 rpm and 4.5o).
Cytodex 1
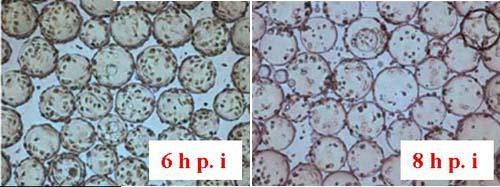
Cytodex 3
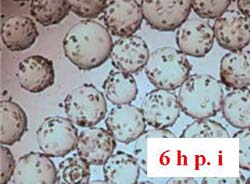
Figure 13. Morphology of Vero cells after attachment to microcarriers. 6 h and 8 h after inoculation.
Microcarrier culture of Vero cells in serum-free conditions in Spinner Flask
Vero cells can also be cultured in microcarriers in roller bottles. As shown in Figure 14, under serum-free conditions, substantially the same maximum cell density can be obtained in both WAVE and rotary flask culture systems. Compared to Cytodex 3, Cytodex 1 has a larger surface area and thus a higher cell density. Vero cells were cultured in the WAVE Bioreactor system and the cells reached confluence 4 days after inoculation. We observed that cells grew rapidly on both microcarriers without a lag phase (Figure 14); cells grew faster in the WAVE reactor than in rotary bottles.
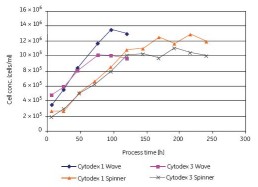
Figure 14. Comparison of Vero cells using Cytodex 1 and Cytodex 3 serum-free cultures in the WAVE Bioreactor system and in the spinner flasks, respectively.
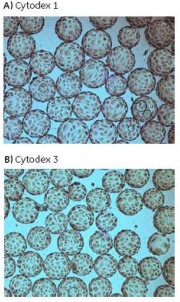
Figure 15 shows the cell morphology of Vero cells after 4 days of culture on Cytodex 1 and Cytodex 3.
Transparent Cytodex microcarriers can be directly microscopically examined without staining, and trypan blue staining can be used to quickly see if cells reach confluence (Figure 16). The intact cell membrane of living cells will block the trypan blue dye and prevent the microcarriers from being stained. Cell-free microcarriers are easily stained, so defects or voids in the cell layer can be easily seen.
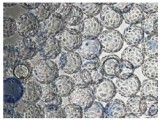
Figure 16. Vero cells confluent on Cytodex 3 in the WAVE Bioreactor system were visualized by trypan blue staining.
in conclusion
This study found that the WAVE Bioreactor system is a universal bioreactor that can be successfully used to culture MDCK and Vero cells in Cytodex microcarriers. MDCK and Vero cells have high microcarrier adherence rates. We found that the WAVE Bioreactor system and the roller bottle have similar maximum cell densities for MDCK and Vero cells, but have a faster growth rate in WAVE. For microcarrier cultures, the recommended optimal working volume is 20% to 80% of the maximum Cellbag working volume.
MDCK cells
· The maximum cell density obtained in this study was 3×10 6 cells/ml, which was obtained under similar growth conditions using a roller bottle.
The cell density is similar.
· We used a similar shaking mixing condition to successfully scale the microcarrier culture from 2 L to 10 L culture bags.
Vero cell
· We optimized the inoculation adherence procedure for Vero cells, successfully obtaining more than 80% under serum-free conditions
Cell adherence rate.
· Vero cells were successfully cultured on Cytodex 1 and 3 in serum-free medium to obtain a uniform cell distribution, and finally the cells reached confluence on the microcarriers.
· Under serum-free conditions, Vero cells grow to a maximum density of approximately 1.4×10 6 cells/ml. Cell density is similar to that of Vero cells grown in roller bottles, and WAVE has a faster growth rate.
Rongcheng Jingyi Oceanic Technology Company Limited , https://www.jingyifoods.cn