[China Pharmaceutical Network Technology News] The domestic medical industry's application of 3D printing technology began in the late 1980s, initially used to quickly manufacture 3D medical models. At that time, 3D printing technology was mainly used to help doctors communicate with patients and accurately. Determine the condition and plan for surgery. It can be said that China's exploration of the application of 3D printing technology in the medical industry has a long history, and it is accompanied by the development of 3D printing technology. 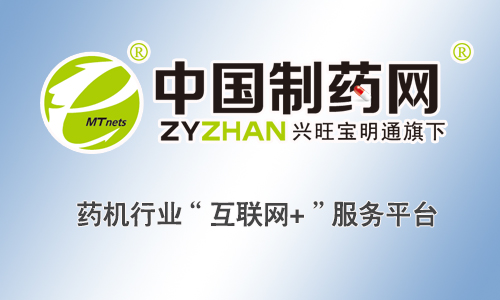
3D printing drugs (Source: Baidu) In recent years, with the development of 3D printing technology and the increasing demand for personalized and personalized medical treatment, 3D printing technology has been significantly developed in terms of breadth and depth in the medical industry. In terms of the breadth of applications, the rapid development of the original medical model, and the development of 3D printing directly to the manufacture of hearing aid housings, implants, complex surgical instruments and 3D printing drugs. In terms of depth, medical devices that are inanimate by 3D printing are developing in the direction of printing biologically active artificial tissues and organs.
The main applications of these medical industries and the main 3D technologies and materials used in these applications can be reflected on one map:
A picture to understand the main application of 3D printing in the medical industry
3D printed medical model and surgical guide
Three-dimensional modeling is performed according to the patient's CT or MRI data before surgery, and then the model is printed out through a 3D printer to obtain a medical model. The main function of the 3D printed medical model is to allow the doctor to visually see the three-dimensional structure of the surgical site before surgery, which helps doctors plan the surgical plan. Especially for complex surgery, it helps to reduce the risk of surgery and improve the success rate of surgery. Surgical guides are an important tool for doctors to assist in surgery during surgery. 3D printing technology is especially suitable for the manufacture of shaped or personalized guides.
From orthopedic surgery to heart surgery to liver surgery... More and more operations are beginning with 3D printed medical models. For example, in 2015, the team of Professor Peng Zhihai, director of the General Surgery Center of Shanghai First People's Hospital, used 3D printing technology to conduct a living liver transplant for a patient with congenital autoimmune cirrhosis and portal hypertension from Guizhou. In order to accurately develop a surgical plan before surgery, experts thought of 3D printing technology. 3D printing presents the patient's hepatobiliary pancreas and corresponding lesions in front of the doctor in a 1:1 "physical" form. By accurately assessing the three-dimensional relationship between the extent of the lesion and the adjacent organ tissue, the team of experts determined that the patient was resected 307. Gram of the liver. During liver resection, the expert brings the model into the operating room for real-time comparison during surgery. By adjusting the 3D printed model and placing it in the best anatomical position, it provides intuitive real-time navigation for critical steps of the operation, and quick identification of key parts. Positioning; by accurately positioning the lesions, blood vessels, and guiding the engagement of important vessels in real time, the accuracy of surgery is improved, and the risk of surgery is effectively reduced.
The precise design of the 3D printed surgical guide is an important guarantee for the success of the operation. Shanghai Yidong Medical Technology Co., Ltd. uses the internationally leading SSM_Knee® technology in the field of orthopedic surgery guides to perform three-dimensional statistical modeling (SSM) and three-dimensional force line measurement from multiple negative-weight X-ray data. Analysis, simulation of the osteotomy plane, artificial total knee arthroplasty on the computer, the implementation of the osteotomy guide in the virtual design surgery and the use of medical materials for 3D printing. During the operation, the doctor only needs to attach the guide plate to the joint surface and then perform the positioning and osteotomy. The accuracy is higher than the traditional method, the human factor is avoided, the operation is simple, and the marrow cavity is not damaged.
3D printing rehabilitation equipment
The true value of 3D printing for the rehabilitation of insole, bionic hand, hearing aid and other rehabilitation equipment is not only to achieve precise customization, but also to make accurate and efficient digital manufacturing technology instead of manual production, shortening the production cycle. Let us take the hearing aid housing industry that has already achieved mass customization of 3D printing as an example. In the traditional way, the technician needs to make an injection mold through the patient's ear canal model. The plastic product is then obtained by ultraviolet light. The final shape of the hearing aid is obtained by drilling the sound hole and manually processing the plastic product. If something goes wrong during this process, you will need to recreate the model. The process of making a hearing aid using a 3D printer begins with the design of the silicone mold or impression of the patient's ear canal. This step is done by a 3D scanner. The CAD software is then used to convert the scanned data into a design file readable by the 3D printer. Designers can modify 3D images through software and create final product shapes. The EnvisionTec printer can print 65 hearing aid housings or 47 hearing aid models in approximately 60 to 90 minutes.
3D printed implant
Bone defects, maxillofacial injuries, skull repairs, etc. due to bone tumors, car accidents, etc., cannot be treated with general repair products, and 3D printing products provide effective solutions, especially for these printed prostheses based on patients. Its own characteristics are tailored to make.
However, the words "tailored" are just one of the meanings of 3D printing technology in the field of implant manufacturing. Another significance of 3D printing technology in this field is that it can print a bionic trabecular micropore structure integrated with the implant, thereby facilitating the growth of human bones. This meaning also exists in 3D printed standardized implants. In the past, trabecular bone structure was achieved by coating on the surface of the implant, and the long-term survival rate of the prosthesis could not be guaranteed. In 2015, the 3D printed artificial hip joint developed by Professor Zhang Ke from the Peking University Third Hospital and Ikang Yicheng Co., Ltd. was approved by the State Food and Drug Administration and became the first 3D printed implant in China.
However, common implant 3D printed materials lack versatility, which limits their use in the treatment and repair of defects caused by orthopedic diseases (eg, bone tumors). The Biomaterials Research Center of the Shanghai Institute of Ceramics, Chinese Academy of Sciences has made progress in this field. The research center is mainly engaged in the research of 3D printing multifunctional bioactive ceramics for bone repair and treatment. Using 3D printing technology, the research team designed a variety of experimental protocols, including the use of nutrients, biomimetic structures and functional interfaces, and thermal therapy to develop new and versatile materials that combine treatment and repair.
3D printing drugs
The impact of 3D printing technology on pharmaceuticals is mainly reflected in four aspects: one is to realize the personalized customization of the active ingredients of the drug; the other is to customize the dosage of the dose to provide individualized treatment plans for patients. This layer-by-layer printing method allows different coatings to be tightly bonded to one another so that the maximum dose of a substance can be placed in a single tablet. In this way, the patient can swallow a small or small number of tablets; the third is to personalize the shape. This may be a good idea for children who don't like to take medicine. Through 3D printing technology, various interesting shapes are printed, and the baby is taken to take medicine; the fourth is to make the drug have a special microstructure through 3D printing technology, and improve the release behavior of the drug, thereby improving the efficacy and reducing side effects. For example, in 2015, the US Food and Drug Administration (FDA) approved the first tablets made entirely in 3D printing worldwide. The drug, called Spritam, was developed by Aprecia Pharmaceuticals Inc. in the United States for the treatment of patients with epilepsy. The most important significance of Zipredose3D printing technology used by Aprecia is that it can rapidly disintegrate high-dose drugs in a small amount of water, which brings great convenience to patients at the time of onset.
Biological 3D printing of tissues and organs
The application development time point of 3D printing in the medical field can be presented in a chart. Among them, bio-3D printing has the largest proportion on the chart: biomedical implant technology is gradually maturing in 2013-2018, and in-situ bio-manufacturing technology began to appear and mature in 2013-2022. In 2013-2032, 3D printed complete human organs Getting better.
Although the biological 3D printing organs that are currently appearing are not fully functional and structurally intact organs, they have begun to play a role in drug screening tests and disease research. The clinical conversion rate of common drug screening technology is low, and the best drug test object is actually the human body. However, this practice is not realistic, because one person can not undertake the initial screening of drugs, and secondly, the individual differences are large and the body structure is complex. The screening of human cells in vitro to construct drugs is an effective alternative to the human body. For example, Hangzhou Jienuofei's mass-produced 3D printing liver unit has been used by Merck Pharmaceuticals for drug toxicity testing. The liver is an important organ responsible for drug toxicity, and the demand for artificial liver is also large. The adult liver consists of 5 to 1 million units called hepatic lobules, which are the basic unit of liver structure and function. The preparation of liver units by mimicking the hepatic lobular structure is a key step in the manufacture of artificial liver. The 3D printed tissue and pathological model of human cells can accurately reflect the pharmacological activities of chemical and biological drugs in the human body, thereby improving the success rate of drug screening.
3D printing and stomatology
The cost of dental restoration and treatment is an important factor for dental clinics and laboratories. Many prescient dental clinics and laboratories have introduced digital dental technology to improve efficiency and reduce costs. In recent years, dental restoration based on software design has become popular, and many dental clinics, laboratories or denture manufacturers have introduced 3D printing technology. Digital dental technology combined with 3D printing brings high precision, low cost, high efficiency to the dental industry, as well as oral data consistent with a standardized production chain. 3D Science Valley believes that the more important significance of digital dental technology, including 3D printing, is to reduce the time for doctors to make dental products such as models and dentures, and to return to the diagnosis of oral diseases and the implementation of oral surgery itself. For dental technicians, although they are far away from the doctor's office, as long as the patient's oral data is obtained, accurate dental products can be customized according to the doctor's requirements. The flow and main application of 3D dental products can be illustrated by the following diagram:
The nichrome alloy from which the tool is made is a difficult-to-machine material, and it is difficult to manufacture the surgical tool using conventional machining methods, and it takes a long time and is costly. In this case, it is more suitable to manufacture using metal 3D printing technology.
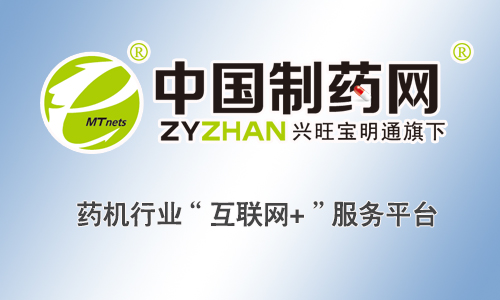
3D printing drugs (Source: Baidu)
The main applications of these medical industries and the main 3D technologies and materials used in these applications can be reflected on one map:
A picture to understand the main application of 3D printing in the medical industry
3d printing in medical industry
3D printed medical model and surgical guide
Three-dimensional modeling is performed according to the patient's CT or MRI data before surgery, and then the model is printed out through a 3D printer to obtain a medical model. The main function of the 3D printed medical model is to allow the doctor to visually see the three-dimensional structure of the surgical site before surgery, which helps doctors plan the surgical plan. Especially for complex surgery, it helps to reduce the risk of surgery and improve the success rate of surgery. Surgical guides are an important tool for doctors to assist in surgery during surgery. 3D printing technology is especially suitable for the manufacture of shaped or personalized guides.
From orthopedic surgery to heart surgery to liver surgery... More and more operations are beginning with 3D printed medical models. For example, in 2015, the team of Professor Peng Zhihai, director of the General Surgery Center of Shanghai First People's Hospital, used 3D printing technology to conduct a living liver transplant for a patient with congenital autoimmune cirrhosis and portal hypertension from Guizhou. In order to accurately develop a surgical plan before surgery, experts thought of 3D printing technology. 3D printing presents the patient's hepatobiliary pancreas and corresponding lesions in front of the doctor in a 1:1 "physical" form. By accurately assessing the three-dimensional relationship between the extent of the lesion and the adjacent organ tissue, the team of experts determined that the patient was resected 307. Gram of the liver. During liver resection, the expert brings the model into the operating room for real-time comparison during surgery. By adjusting the 3D printed model and placing it in the best anatomical position, it provides intuitive real-time navigation for critical steps of the operation, and quick identification of key parts. Positioning; by accurately positioning the lesions, blood vessels, and guiding the engagement of important vessels in real time, the accuracy of surgery is improved, and the risk of surgery is effectively reduced.
The precise design of the 3D printed surgical guide is an important guarantee for the success of the operation. Shanghai Yidong Medical Technology Co., Ltd. uses the internationally leading SSM_Knee® technology in the field of orthopedic surgery guides to perform three-dimensional statistical modeling (SSM) and three-dimensional force line measurement from multiple negative-weight X-ray data. Analysis, simulation of the osteotomy plane, artificial total knee arthroplasty on the computer, the implementation of the osteotomy guide in the virtual design surgery and the use of medical materials for 3D printing. During the operation, the doctor only needs to attach the guide plate to the joint surface and then perform the positioning and osteotomy. The accuracy is higher than the traditional method, the human factor is avoided, the operation is simple, and the marrow cavity is not damaged.
3D printing rehabilitation equipment
The true value of 3D printing for the rehabilitation of insole, bionic hand, hearing aid and other rehabilitation equipment is not only to achieve precise customization, but also to make accurate and efficient digital manufacturing technology instead of manual production, shortening the production cycle. Let us take the hearing aid housing industry that has already achieved mass customization of 3D printing as an example. In the traditional way, the technician needs to make an injection mold through the patient's ear canal model. The plastic product is then obtained by ultraviolet light. The final shape of the hearing aid is obtained by drilling the sound hole and manually processing the plastic product. If something goes wrong during this process, you will need to recreate the model. The process of making a hearing aid using a 3D printer begins with the design of the silicone mold or impression of the patient's ear canal. This step is done by a 3D scanner. The CAD software is then used to convert the scanned data into a design file readable by the 3D printer. Designers can modify 3D images through software and create final product shapes. The EnvisionTec printer can print 65 hearing aid housings or 47 hearing aid models in approximately 60 to 90 minutes.
3D printed implant
Bone defects, maxillofacial injuries, skull repairs, etc. due to bone tumors, car accidents, etc., cannot be treated with general repair products, and 3D printing products provide effective solutions, especially for these printed prostheses based on patients. Its own characteristics are tailored to make.
However, the words "tailored" are just one of the meanings of 3D printing technology in the field of implant manufacturing. Another significance of 3D printing technology in this field is that it can print a bionic trabecular micropore structure integrated with the implant, thereby facilitating the growth of human bones. This meaning also exists in 3D printed standardized implants. In the past, trabecular bone structure was achieved by coating on the surface of the implant, and the long-term survival rate of the prosthesis could not be guaranteed. In 2015, the 3D printed artificial hip joint developed by Professor Zhang Ke from the Peking University Third Hospital and Ikang Yicheng Co., Ltd. was approved by the State Food and Drug Administration and became the first 3D printed implant in China.
However, common implant 3D printed materials lack versatility, which limits their use in the treatment and repair of defects caused by orthopedic diseases (eg, bone tumors). The Biomaterials Research Center of the Shanghai Institute of Ceramics, Chinese Academy of Sciences has made progress in this field. The research center is mainly engaged in the research of 3D printing multifunctional bioactive ceramics for bone repair and treatment. Using 3D printing technology, the research team designed a variety of experimental protocols, including the use of nutrients, biomimetic structures and functional interfaces, and thermal therapy to develop new and versatile materials that combine treatment and repair.
3D printing drugs
The impact of 3D printing technology on pharmaceuticals is mainly reflected in four aspects: one is to realize the personalized customization of the active ingredients of the drug; the other is to customize the dosage of the dose to provide individualized treatment plans for patients. This layer-by-layer printing method allows different coatings to be tightly bonded to one another so that the maximum dose of a substance can be placed in a single tablet. In this way, the patient can swallow a small or small number of tablets; the third is to personalize the shape. This may be a good idea for children who don't like to take medicine. Through 3D printing technology, various interesting shapes are printed, and the baby is taken to take medicine; the fourth is to make the drug have a special microstructure through 3D printing technology, and improve the release behavior of the drug, thereby improving the efficacy and reducing side effects. For example, in 2015, the US Food and Drug Administration (FDA) approved the first tablets made entirely in 3D printing worldwide. The drug, called Spritam, was developed by Aprecia Pharmaceuticals Inc. in the United States for the treatment of patients with epilepsy. The most important significance of Zipredose3D printing technology used by Aprecia is that it can rapidly disintegrate high-dose drugs in a small amount of water, which brings great convenience to patients at the time of onset.
Biological 3D printing of tissues and organs
The application development time point of 3D printing in the medical field can be presented in a chart. Among them, bio-3D printing has the largest proportion on the chart: biomedical implant technology is gradually maturing in 2013-2018, and in-situ bio-manufacturing technology began to appear and mature in 2013-2022. In 2013-2032, 3D printed complete human organs Getting better.
Although the biological 3D printing organs that are currently appearing are not fully functional and structurally intact organs, they have begun to play a role in drug screening tests and disease research. The clinical conversion rate of common drug screening technology is low, and the best drug test object is actually the human body. However, this practice is not realistic, because one person can not undertake the initial screening of drugs, and secondly, the individual differences are large and the body structure is complex. The screening of human cells in vitro to construct drugs is an effective alternative to the human body. For example, Hangzhou Jienuofei's mass-produced 3D printing liver unit has been used by Merck Pharmaceuticals for drug toxicity testing. The liver is an important organ responsible for drug toxicity, and the demand for artificial liver is also large. The adult liver consists of 5 to 1 million units called hepatic lobules, which are the basic unit of liver structure and function. The preparation of liver units by mimicking the hepatic lobular structure is a key step in the manufacture of artificial liver. The 3D printed tissue and pathological model of human cells can accurately reflect the pharmacological activities of chemical and biological drugs in the human body, thereby improving the success rate of drug screening.
3D printing and stomatology
The cost of dental restoration and treatment is an important factor for dental clinics and laboratories. Many prescient dental clinics and laboratories have introduced digital dental technology to improve efficiency and reduce costs. In recent years, dental restoration based on software design has become popular, and many dental clinics, laboratories or denture manufacturers have introduced 3D printing technology. Digital dental technology combined with 3D printing brings high precision, low cost, high efficiency to the dental industry, as well as oral data consistent with a standardized production chain. 3D Science Valley believes that the more important significance of digital dental technology, including 3D printing, is to reduce the time for doctors to make dental products such as models and dentures, and to return to the diagnosis of oral diseases and the implementation of oral surgery itself. For dental technicians, although they are far away from the doctor's office, as long as the patient's oral data is obtained, accurate dental products can be customized according to the doctor's requirements. The flow and main application of 3D dental products can be illustrated by the following diagram:
Dental application
3D printing and medical device manufacturers <br> <br> manufacture of medical devices and other products, new product development stage need to create product prototypes for design verification. 3D printing is an economical and fast way to prototype a product. It is usually done by using plastic 3D printing technology such as FDM or SLA to complete rapid prototyping. The potential of metal 3D printing technology in the field of medical devices has surpassed the prototype to undertake the manufacturing tasks of complex surgical instruments. For example, in the knee anterior cruciate ligament injury repair surgery, the doctor first removes the remaining anterior cruciate ligament and then accurately replaces the upper graft ligament. To ensure accurate and minimally invasive surgery, doctors need a sophisticated and special surgical tool. The nichrome alloy from which the tool is made is a difficult-to-machine material, and it is difficult to manufacture the surgical tool using conventional machining methods, and it takes a long time and is costly. In this case, it is more suitable to manufacture using metal 3D printing technology.
Insulin Syringes Needle,Disable Syringe,Monoject Syringe,10 Ml Syringe
FOSHAN PHARMA CO., LTD. , https://www.fs-pharma.com